Straßen sanieren mit Kaltfräsen 20.01.2011, 16:36
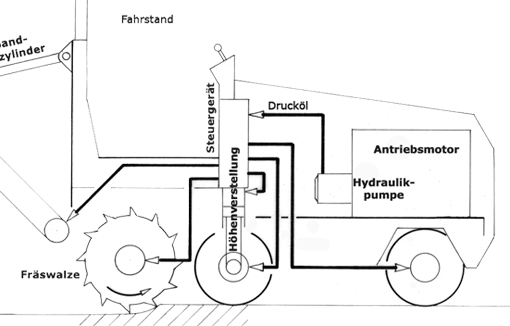
Bei der Sanierung von Straßen ist Kaltfräsen der 1. Arbeitsschritt. Er trägt Asphaltschichten verschiedener Dicke ab. Hoch verschleißfeste, mit Hartmetallmeißeln ausgestattete Fräswalzen lösen die Straßendecke. Erst danach wird das neue Straßenmaterial eingebaut.
Kaltfräsen
Beim Sanieren von Straßen wird im ersten Schritt der beschädigte Belag abgetragen. Das Kaltfräsen ist das gängige moderne Verfahren dafür.
Bild: Fräswalze mit montierten Hartmetallmeißeln (Bild WIRTGEN)
Das Funktionsprinzip: Eine rotierende Fräswalze wird auf die erforderliche Frästiefe abgesenkt und löst den Straßen- beziehungsweise Wegbelag, der entweder aus Asphalt oder Beton besteht. Bei günstigen Voraussetzungen kann eine Kaltfräse mit 2,20 Meter Fräsbreite bis zu 1 200 Tonnen Asphaltbelag pro Stunde ausbauen. Das entspricht der Ladekapazität von etwa 60 Lkw. Das Fräsgut wird je nach Bauverfahren und logistischen Anforderungen der Baustelle entweder mit einem Ladeband auf einen Lkw verladen oder seitlich abgelegt beziehungsweise in der verbleibenden Frässpur belassen und anschließend per Radlader auf Lkw verladen. Das so gewonnene Material kann direkt auf der Baustelle als Auskofferung wiederverwendet werden.
Inzwischen gibt es auch kostengünstige Verfahren, die dieses Recyclingmaterial für den Unterbau verwenden. Nach dem Abfräsen der Straßendecke wird das Granulat nach Körnungen sortiert, erwärmt, mit Zusatzstoffen angereichert und wieder eingebaut. Die Zusatzstoffe sorgen dafür, dass das spröde gewordene Altmaterial beim Erwärmen wieder geschmeidig wird und beim Verlegen eine dichte Schicht bildet.
Was den Antrieb der Einzelaggregate betrifft, ist die Verwandtschaft von Straßenfräsen mit anderen Baumaschinen nicht zu verkennen.
Den Antrieb liefert ein Dieselmotor, an den Hydraulikpumpen angeflanscht sind. Sie erzeugen Drucköl, das Verbrauchern wie Arbeitszylindern oder Hydromotoren die Energie liefert.
Die wichtigsten Verbraucher sind das Fahrwerk, die Fräswalze und das Ladeband. Die Fräswalze selbst ist in einem rundum dichten Kasten untergebracht, der nur gegen das Ladeband hin offen ist. Während des Fräsvorganges lösen die Meißel den Belag und granulieren ihn zu kleinstückigem, wiederverwendbarem Material.
Bild: Fräswalze bei der Arbeit. Der abgefräste und granulierte Asphalt gelangt auf ein Förderband (Bild WIRTGEN)
Fräsverfahren
Der Begriff Kaltfräsen unterscheidet sich vom Heißfräsen, das noch bis 1980 angewandt wurde. Das Arbeitsprinzip entsprach bereits dem des heutigen Kaltfräsens, allerdings musste die Deckschicht vor dem Fräsen erwärmt werden. Wegen des enormen Energieaufwands für das Erhitzen der Decke ist es aus heutiger Sicht unter Umwelt- und Kostengesichtspunkten nicht mehr tragbar. Mit der Entwicklung neuer Fräsmeißel aus hochfesten Hartmetallen, deutlich leistungsfähigerer Antriebstechnik und stabilerer Gesamtkonstruktion halten die Maschinen den beim Kaltfräsen auftretenden, im Vergleich zum Heißfräsen sehr viel höheren Kräften besser stand. Darüber hinaus ermöglicht die neue Fräsen-Generation größere Arbeitstiefen bis zu 35 Zentimeter.
Bei der Maschinengröße unterscheidet man zwei Typen. Kleinfräsen haben Arbeitsbreiten zwischen 35 und 130 Zentimeter. Sie sind besonders kompakt in ihrer Bauweise und dadurch einfach zur Baustelle zu transportieren. Sie arbeiten vorwiegend mit Radfahrwerken und verfügen über kleine Wenderadien. Die Fräswalze ist am Heck der Maschine angeordnet. Das Fräsgut wird hinter der Walze abgelegt beziehungsweise mit einem Überladeband entgegen der Fahrtrichtung abtransportiert (so genannter »Hecklader«, siehe Bild).
Großfräsen werden meistens mit Kettenlaufwerken, einer in Maschinenmitte angeordneten Fräswalze sowie einer nach vorn auskragenden Fräsgut-Verladeeinrichtung konzipiert (Frontlader, siehe Bild, WIRTGEN).
Grundaufbau der Kaltfräse
Tragender Teil der Fräse ist das Chassis, eine Schweißkonstruktion, auf der die Funktionsmodule und Aufbauten montiert sind. Integriert sind die Tanks für Hydrauliköl, Dieselkraftstoff und Wasser. Aus dem Wassertank wird eine Wassersprühanlage versorgt, die Staubentwicklung während der Fräsarbeit verhindert und die Fräsmeißel kühlt, was deren Lebensdauer erhöht.
Der Fahrerstand nimmt die Bedienpulte und Fahrersitze auf. Bei größeren Maschinen sind diese in Neigung und Höhe verstellbar. Außerdem können sie zum Teil seitlich über die Außenkante der Maschine hinaus verschoben werden.
Angetrieben werden die Fräsen in der Regel durch Vier-oder Sechs-Zylinder-Dieselmotoren. Je nach Größe der Maschine reicht die Leistung von etwa 30 bis weit über 700 kW (40 bis 950 PS). Eine automatische Leistungsregelung stimmt den Vorschub in Abhängigkeit von Motor- und Fräswalzenleistung optimal ab. Kleinfräsen werden auch mit Elektromotoren (für Netzspannung 400 Volt) angeboten.
Bei Kleinfräsen besteht das Fahrwerk aus drei oder vier Rädern, je nach Version mit hydraulischem Vorderrad- oder Allradantrieb. Das Arbeiten mit »Hundegang« lässt auch das Heranfahren der Maschine dicht an Wände, Gehsteige und sonstige Kanten zu.
Bild: Lenkungsarten
Großfräsen bewegen sich auf vier Kettenlaufwerken (mit jeweils eigenen Hydromotoren sowie stufenlosen Hydroverstellpumpen) fort. Eine hydraulische Höhenverstellung mit großen Hubwegen stellt eine große Bodenfreiheit und damit Manövrierfähigkeit sicher. Große Einschlagswinkel und Vier-Ketten-Lenkung machen die Maschine wendig.
(Bild WIRTGEN)